- Autor Original: Steve Osborne, director de ventas ferroviarias de PPG Protective and Marine Coatings. Ha estado en el negocio de los recubrimientos durante más de 35 años. [email protected]
- Traducido y Editado por: IARCOR INTERNACIONAL
- Fuente: https://www.paintsquare.com/
Pocas imágenes capturan mejor la esencia de la Revolución Industrial que las de la industria ferroviaria. Desde vías talladas en las extensiones de la nueva frontera hasta una locomotora de gran tamaño que ondeaba vapor mientras cruzaba las estructuras metálicas sobre un desfiladero de un río, estas imágenes evocan una sensación de determinación y fuerza.
A medida que pasan los años, esa fuerza se vería probada por la presión del consumidor y las fuerzas económicas mundiales; sin embargo, la resistencia de la industria ferroviaria se vería reforzada por la resistencia de los revestimientos que protegen los vagones y los activos relacionados. Originalmente fueron elegidos para proteger contra la exposición exterior a los elementos y la corrosión, los recubrimientos se volvieron confiables para muchas más aplicaciones
Impulsadas por la Revolución Industrial, cada vez más industrias reconocieron los beneficios de transportar sus mercancías por ferrocarril. Para acomodarlos, se desarrollaron varios tipos de vagones de carga (por ejemplo, gondola, tolva, tanque, etc). Esto provocó una mayor preocupación por los revestimientos de los vagones de mercancías y la necesidad de crear una barrera protectora impermeable entre el vagón y los propios productos básicos. La industria de los recubrimientos tendría que adaptarse a estos cambios tanto como la industria ferroviaria, y el flujo y reflujo de la demanda de productos básicos afectaría las inversiones en investigación y desarrollo de mejoras de recubrimientos y avances tecnológicos.
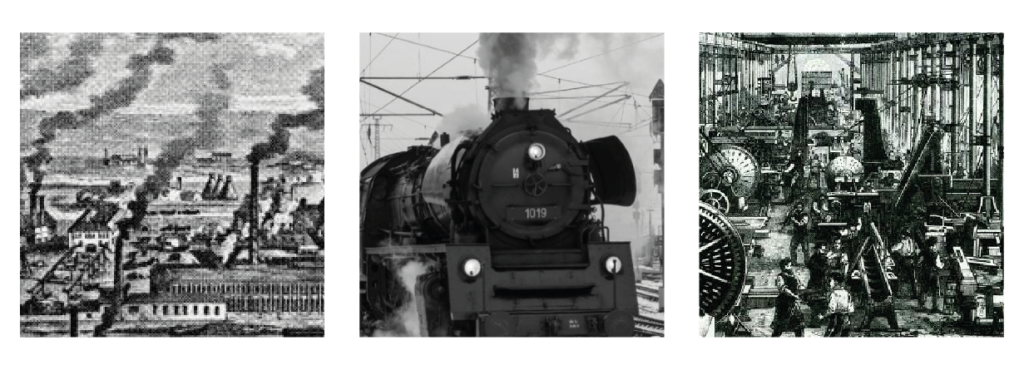
UN RECUBRIMIENTOS NO SE ADAPTA A TODAS LAS FUNCIONES
A lo largo del siglo XX, la industria de los revestimientos siguió evolucionando para abordar los desafíos del revestimiento de los vagones de mercancías. El enfoque inicial de los revestimientos para esta industria fue direccionada a diferentes aplicaciones con soluciones similares. Como ejemplo los vagones cisterna, tenían una solución de recubrimientos genérica aplicada en su interior independientemente del producto que transporta, estos vagones cisterna también podrían llevar diferentes tipos de productos durante su vida útil, por lo tanto el revestimiento interno estaría en contacto con unas gran cantidad de materiales.
De manera similar, con otros tipos de vagones de carga, se aplicó una única solución desde el principio para abordar cualquier producto básico que el propietario o arrendatario debía transportar. Esto requirió una solución de recubrimientos de “talla única” para soportar todas las aplicaciones posibles.
Pero a lo largo de los años, los propietarios de ferrocarriles y los arrendatarios utilizarían cada vez más vagones de carga que se dedicaban a un producto en particular, por lo que la necesidad de tener una única solución de revestimiento diseñada para todos, probablemente más resistente, más cara y más difícil de aplicar de lo que tenía que ser, se volvió menos necesario. La industria de los revestimientos, en cambio, desarrolló cada vez más soluciones de alta tecnología para revestimientos de vagones y aplicaciones específicas.
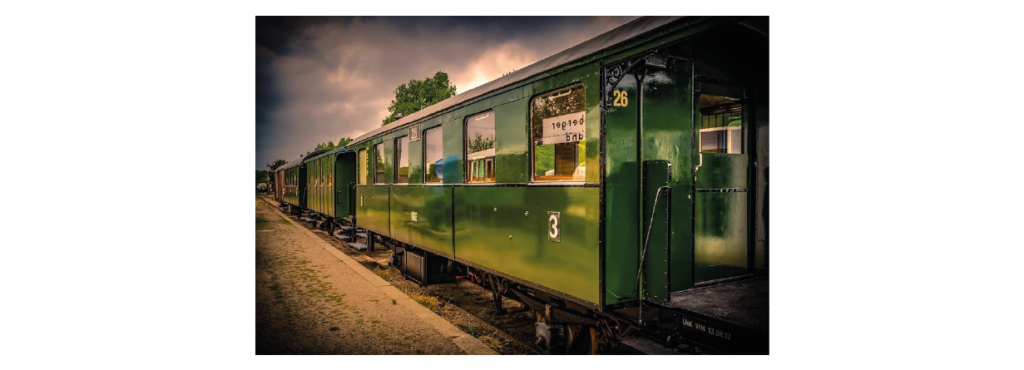
CUBRIENDO LAS NECESIDADES DE LA INDUSTRIA
Independientemente de las técnicas y como fue la aplicación, la solución para la industria de los vagones de ferrocarril, existían ciertos requisitos básicos que la industria de los recubrimientos debía cumplir. Estos se mantuvieron constantes a lo largo de los años.
La resistencia a la corrosión (proteger el exterior del vagón de los elementos) era un requisito clave. Otro requisito era proteger los revestimientos internos de los vagones de carga de la exposición a la carga corrosiva y mantener la pureza de la carga (por ejemplo, los gránulos de plástico necesarios para mantener la máxima pureza a fin de optimizar cualquier proceso de fabricación para el que se utilizaría el plástico).
Otro requisito clave para la industria de los vagones de ferrocarril fue minimizar los costos de mantenimiento y mano de obra. Para los propietarios y / o arrendatarios de la industria ferroviaria, el tiempo era dinero, por lo que cuanto menos tiempo tuviera que estar un vagón en el patio para reparaciones o mantenimiento, incluyendo la aplicación o reaplicación de recubrimientos, más propietarios y arrendatarios podrían maximizar el rendimiento y tiempo de actividad y minimizar el tiempo de inactividad
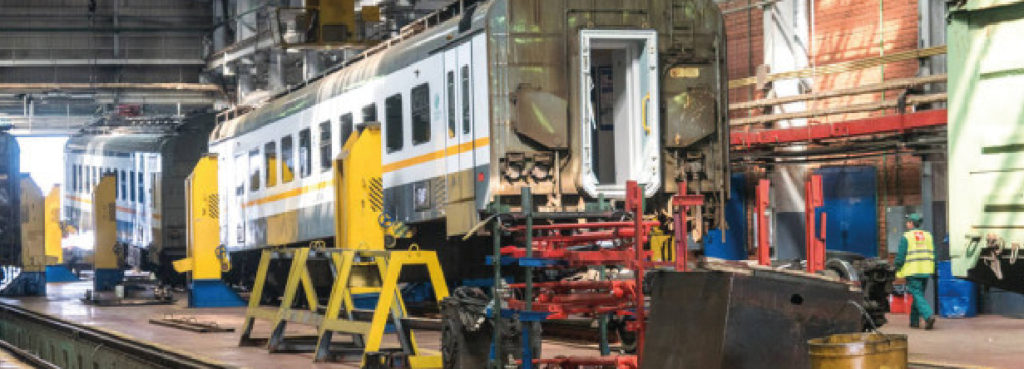
EVOLUCIÓN DE LA INDUSTRIA
A lo largo de la historia, las industrias se han visto obligadas a evolucionar o enfrentarse a la extinción. Algunos de esos avances evolutivos fueron de hecho revolucionarios y otros no lo fueron tanto, requiriendo ajustes menores en equipos o procesos y procedimientos. No fue diferente para la industria ferroviaria. Un avance se produjo a finales de la década de 1980 cuando los propietarios y arrendatarios de vagones de ferrocarril buscaron aumentar la eficiencia y la rentabilidad.
La creación de vagones de carga jumbo tuvo que lograrse sin aumentos significativos del peso bruto del vagón, lo que se hizo disminuyendo el grosor de las paredes de los vagones. Pero la disminución del grosor y el peso de la pared significó una mayor flexibilidad de la estructura del vagón de carga, por lo que la solución de revestimientos correspondiente necesitaba abordar este aumento de flexibilidad sin comprometer la integridad del revestimiento interno protector del vagón.
CUBRIENDO LAS NECESIDADES DE LA INDUSTRIA, EL PROCESO NUNCA TERMINA.
El desarrollo de epoxicos sin solventes, como PPG Amercoat 428 PCLO, proporcionó revestimientos internos flexibles que cumplieron con las necesidades de los nuevos vagones de carga jumbo y se convirtieron en el estándar de la industria durante más de 25 años. Además de ser más flexibles y más resistentes a la abrasión que los recubrimientos epóxicos convencionales, los epóxicos sin solventes también ofrecían numerosos beneficios a los propietarios y arrendatarios. El principal de ellos fue el cumplimiento de las nuevas regulaciones gubernamentales y las restricciones de VOC que obligaron a los proveedores de pintura a desarrollar revestimientos internos para vagones cisterna cada vez más sólidos.
Otro beneficio de la solución de una sola capa para vagones de carga fue un mayor rendimiento para los aplicadores, lo que finalmente redujo los costos de mantenimiento y reparación y aumentó la rentabilidad para los propietarios y arrendatarios. Los epóxicos sin disolventes tampoco eran inflamables y proporcionaban una protección de alto espesor, con fácil limpieza, poco olor durante la aplicación y una estética de alto brillo.
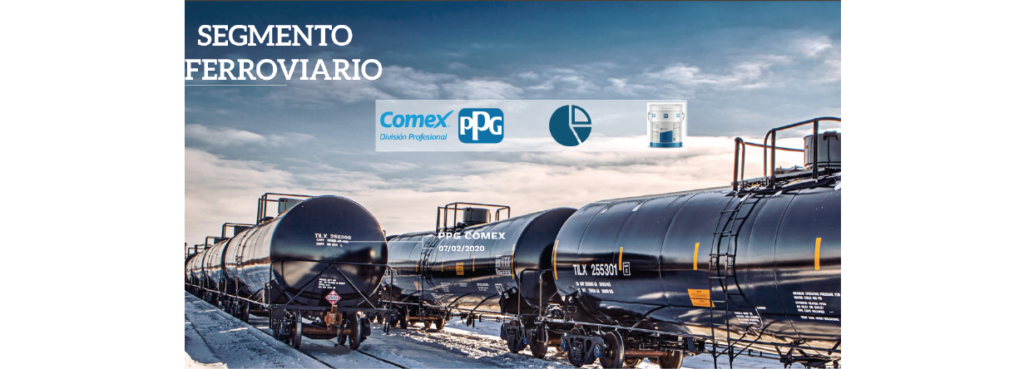
APROVECHAR LA TECNOLOGÍA EXISTENTE
A medida que la industria de los revestimientos continuó trabajando con la industria de los vagones de ferrocarril para crear revestimientos protectores para los vagones de carga, los propietarios de vagones expresaron preocupaciones comparables sobre la protección de la pureza de los productos básicos transportados en vagones cisterna. Para crear una barrera protectora impermeable entre el vagón cisterna y los productos, y para lograr resistencia química, la industria de los recubrimientos desarrolló revestimientos internos protectores para tanques que requerían tres o cuatro capas, con un curado de alta cocción de hasta 200 grados por cada capa. Este fue un proceso laborioso de tres o cuatro días que fue una propuesta costosa para los propietarios de vagones de ferrocarril, ya que provocó que los vagones cisterna estuvieran fuera de servicio durante un período prolongado.
Este curado de alto horneado fue el estándar de la industria durante décadas, pero las nuevas restricciones gubernamentales sobre los compuestos orgánicos volátiles ( VOC s )y la necesidad de reducir los costos de mantenimiento, reparación y mano de obra llevaron a la industria de los recubrimientos a explorar soluciones alternativas para los revestimientos internos de vagones cisterna.
Aprovechando la tecnología existente y el éxito de los epóxicos sin solvente de una sola capa utilizados en los revestimientos de los vagones de carga durante más de 20 años, la industria de los recubrimientos buscó una solución similar que pudiera funcionar en los vagones cisterna. Se desarrollaron productos como PPG Novaguard 890, un recubrimiento epóxico fenólico de novolaca curado con amina, de dos componentes, libre de solventes, que proporciona un revestimiento epóxico de una sola capa que no requiere un curado de alto horneado resistente para vagones cisterna que redujo el proceso de aplicación de cuatro días a solo un día, lo que disminuyó el tiempo de pintura en un 75% y reduciendo los costos de hasta un 25%.
El epoxico PPG Novaguard 890 proporcionó un bajo contenido de VOC para cumplir con las estrictas pautas regulatorias y los productos básicos y mantienen una implica gamas de químicos o productos, que siempre han sido tan importantes para los propietarios y arrendatarios de vagones de ferrocarril. También brindó buena visibilidad, debido a su color claro, excelentes capacidades de llenado de picaduras y menor riesgo de explosión e incendio.
Como señaló Tim Nelson, especialista en ferrocarriles, equipo ferroviario y conformidad en la empresa Philips 66, “El sistema de una sola capa, con un sólido historial de protección de fondos de tanques de crudo, mejoró la tasa de revestimiento de nuestro proyecto de reacondicionamiento de crudo. También fue capaz de fluir fácilmente dentro de los vagones para brindar una cobertura completa, por lo que funcionó muy bien”.
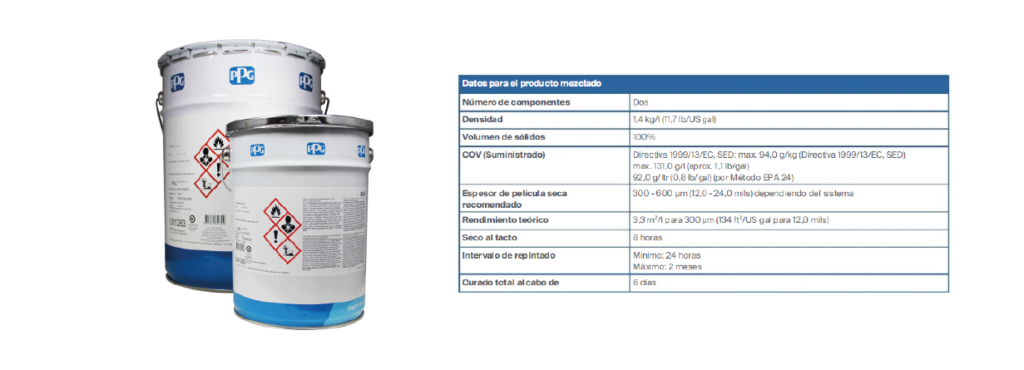
LAS NUEVAS METAS
Desde vagones de carga hasta vagones cisterna, los revestimientos internos siempre han desempeñado un papel fundamental en el mantenimiento de la vida útil de un vagón de ferrocarril. En años más recientes, los propietarios y arrendatarios de ferrocarriles han presionado cada vez más para lograr mejoras en la estética de los vagones mientras optimizan la protección contra la corrosión exterior.
Los productos uretanos aplicados directamente al metal (DTM), incluido el Durethane DTM de PPG, han brindado protección contra la corrosión de alto brillo de larga duración y una excelente retención del color para aplicaciones exteriores de vagones de ferrocarril. Los epóxicos de color estable, que proporcionan una combinación duradera de estética y protección contra la corrosión, también han surgido como soluciones viables y rentables para los vagones de ferrocarril.
Pero ya se trate de uretanos o epoxicos, DTM o sistemas de capas múltiples, los fabricantes de recubrimientos continuarán con su larga tradición de trabajar en estrecha colaboración con los propietarios, arrendatarios y aplicadores para proporcionar nuevas tecnologías de recubrimientos que permitirán a la industria ferroviaria seguir rodando, trabajando y mirando la nueva frontera.
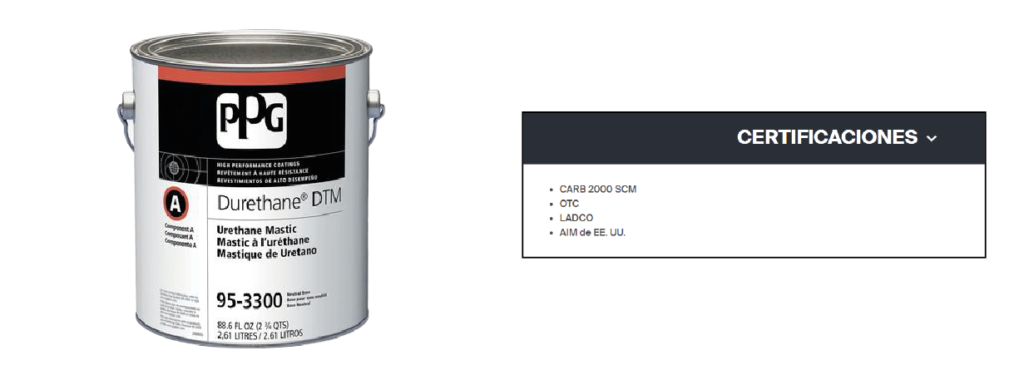