- Autor Original: Manuel Najar, Ingenieros Consultores de V&A, INC.
- Traducido y Editado por: IARCOR INTERNACIONAL
Varios propietarios de tratamiento de agua y aguas residuales se han enfrentado a los efectos de la corrosión biogénica y el deterioro químico del hormigón en sus estructuras. Las evaluaciones de estas estructuras afectadas pueden ayudar a identificar el tipo y el alcance del deterioro. Hay varios métodos de evaluación que se pueden utilizar para determinar la condición existente de una estructura de hormigón revestida o no revestida. Este artículo identificará algunos indicadores importantes de corrosión biogénica y deterioro químico del hormigón, con algunos ejemplos de diferentes áreas del proceso de tratamiento de agua y aguas residuales.
REVISIÓN DE LOS ENTORNOS DE SERVICIO
La mayoría de los entornos de servicio de agua y aguas residuales se pueden dividir en cuatro entornos de servicio: atmosférico interior, atmosférico exterior, exterior enterrado y sumergido.
El tipo de protección requerida para el hormigón dependerá del líquido, sólido o gas al que estará expuesto el hormigón durante el funcionamiento normal de la estructura. Después de clasificar el sustrato que se va a revestir en uno o más de los entornos de servicio, se pueden determinar el material de revestimiento apropiado, la preparación de la superficie y los requisitos de aplicación del revestimiento para proteger las superficies.
Ambientes con alto contenido de cloruro
El concreto puede estar expuesto a ambientes con alto contenido de cloruro, como en vías fluviales con alta salinidad y en ambientes marinos. Además, el hormigón también puede estar expuesto a altas concentraciones de cloruros en la etapa de desinfección del proceso de tratamiento de agua y aguas residuales. Los productos químicos de desinfección como el hipoclorito de sodio, el hipoclorito de calcio y el dióxido de cloro son aguas residuales después de haber sido procesadas mediante un tratamiento primario y secundario. En las grandes plantas de tratamiento de agua y aguas residuales, la dosificación de estos productos químicos se realiza antes de que ingresen a un largo canal sinuoso que normalmente se construye con hormigón. El agua debe viajar a través del canal para permitir suficiente tiempo para una mezcla y desinfección adecuadas. A medida que el agua desinfectada viaja a través del canal, los cloruros comienzan a migrar a través del concreto. Se producirá la migración de cloruros a través del concreto y podría potencialmente comenzar a corroer el acero de refuerzo si no hay una cobertura de concreto insuficiente, la relación agua-cemento es alta y la matriz de concreto no es lo suficientemente densa para evitar la migración de cloruros.
Cuando la humedad y los cloruros llegan al acero de refuerzo, el acero comienza a corroerse y puede perder su integridad estructural. La corrosión del acero de refuerzo causada por los cloruros se ve agravada por el agrietamiento, el desconchado o la poca profundidad de la superficie del concreto es causada por la celda de corrosión creada por el cátodo y el ánodo dentro del acero y el agua (electrolito). El material naranja que se forma en la superficie son depósitos de óxido ferroso. Los cloruros rompen la capa protectora de óxido sobre el acero de refuerzo incrustado en el hormigón, lo que provoca la corrosión del metal.
Cuando se observa un daño en una estructura de hormigón, los propietarios quieren saber el alcance del daño y cuánto costará repararlo.
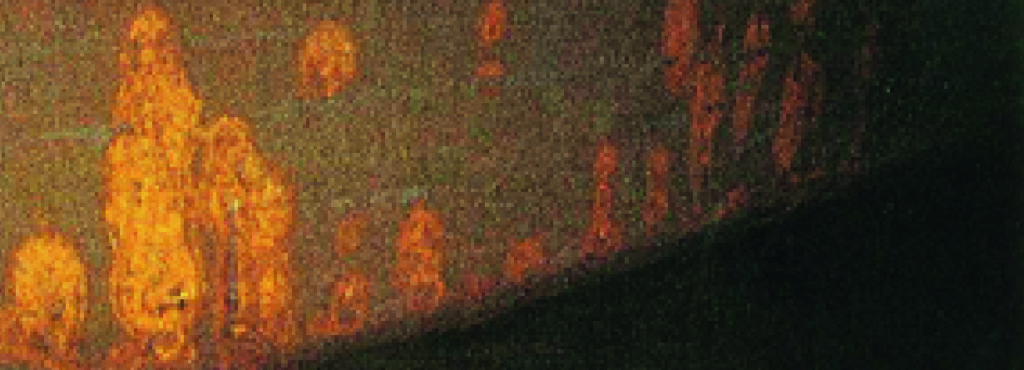
La Figura 1 muestra varias áreas con manchas de corrosión en la pared inferior de un canal de contacto con cloro después de 30 años de servicio. No está claro si el acero de refuerzo corroído que se muestra en la foto es un refuerzo vertical o una longitud de superposición que se dobló hacia arriba desde el refuerzo de la losa del piso. En cualquiera de las opciones de colocación del refuerzo, el acero de refuerzo debe protegerse de una mayor corrosión. La figura 2 es una vista detallada de un nódulo de corrosión que se formó sobre el acero de refuerzo. El tamaño de un nódulo de corrosión puede variar según la longitud y la profundidad del acero de refuerzo que está expuesto o cerca de la superficie.
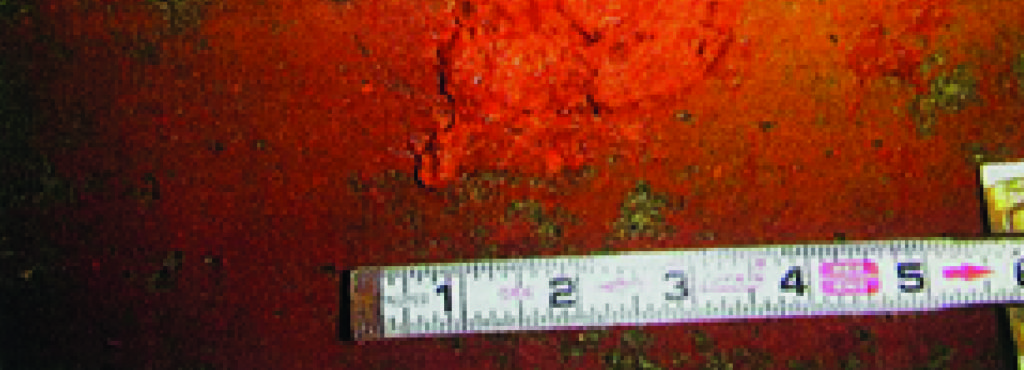
Ambientes de corrosión biogénica
El término “corrosión biogénica de aguas residuales” se utiliza aquí para definir el proceso de corrosión causado por la conversión biológica de gas sulfuro de hidrógeno en ácido sulfúrico en alcantarillas e instalaciones de aguas residuales. La corrosión biogénica de las aguas residuales no debe confundirse con otros procesos de corrosión biológica, comúnmente denominada “corrosión inducida microbiológicamente”, que a menudo puede asociarse con la corrosión por grietas en el suministro de agua y otros sistemas ambientales no asociados con el gas de sulfuro de hidrógeno o las aguas residuales. El hormigón es el material de construcción de aguas residuales más susceptible a la corrosión biogénica. El ácido producido por la bacteria acidithiobacillus hace más destrucción en ambientes atmosféricos interiores, como el espacio de cabeza de estructuras cerradas o en áreas donde el flujo de aguas residuales es turbulento y contiene altos niveles de sulfuros disueltos. Algunas especies de Acidithiobacillus que se encuentran en las alcantarillas son activas a un PH de 1 y pueden destruir completamente las estructuras de hormigón armado si están presentes altas concentraciones de gas sulfuro de hidrógeno.
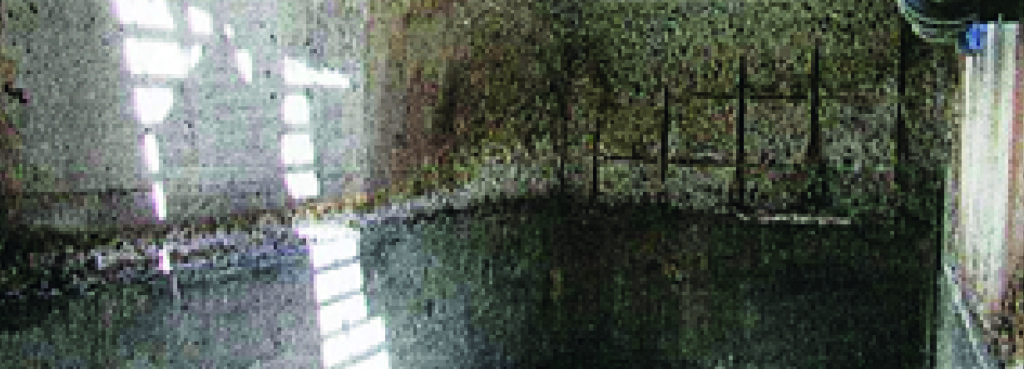
La Figura 3 muestra un ejemplo de corrosión biogénica en el canal afluente de una cuenca de sedimentación primaria en una planta de tratamiento de aguas residuales. Como puede verse, las superficies de hormigón sobre la superficie de las aguas residuales se han deteriorado significativamente debido a la corrosión biogénica. El deterioro del hormigón ha dejado al descubierto el acero de refuerzo y lo ha corroído por completo en algunas zonas donde solo quedan manchas anaranjadas, como se muestra en la Figura 4.
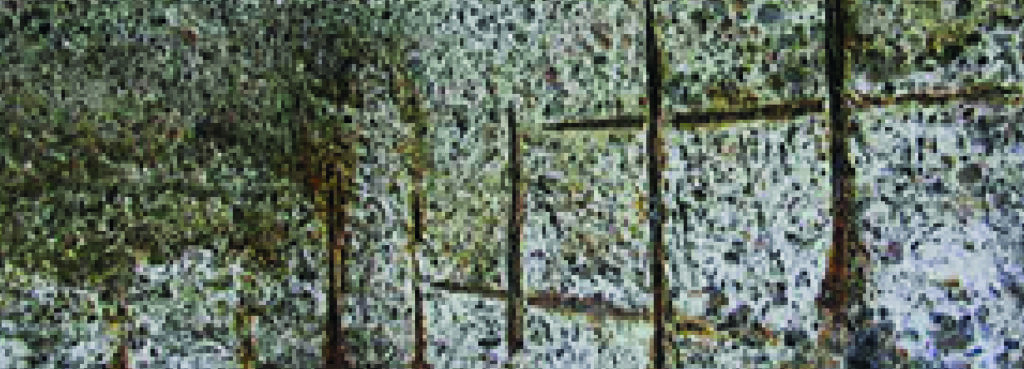
Otra forma de corrosión biogénica puede ser causada por grasas, aceites y grasas en forma de desperdicio de alimentos, que son recolectados por transportistas privados y eliminados en plantas de tratamiento de aguas residuales. Los residuos de alimentos se procesan y se envían a un digestor anaeróbico para mezclarlos con los sólidos y biosólidos del proceso de tratamiento de aguas residuales.
El rápido, el aceite y los ácidos grasos reaccionan con los álcalis en la pasta de cemento y hacen que la pasta de cemento se vuelva blanda y resbaladiza La Figura 5 (p.16) muestra las superficies rugosas de un pedestal de concreto que se limpió con agua a una presión de 4000 psi. El revestimiento existente había fallado en las superficies del piso, pero aún estaba bien adherido e intacto en las paredes.
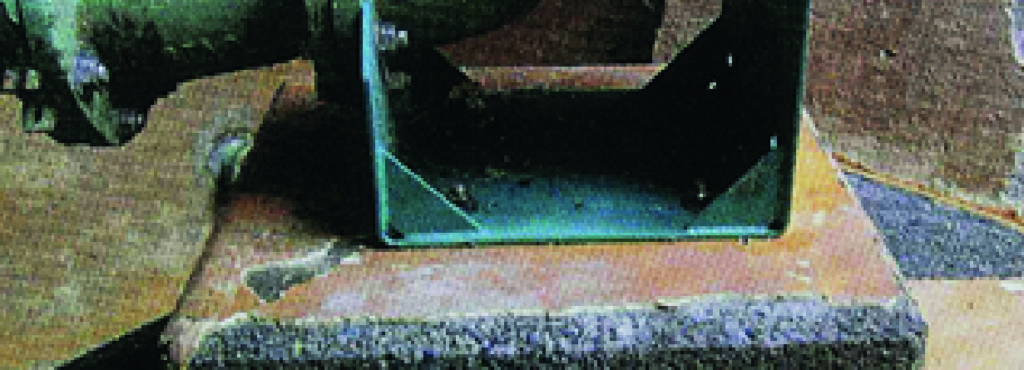
Daños en el área de contención secundaria
Los productos químicos a granel se utilizan ampliamente en varias etapas de las plantas de tratamiento. En las plantas de tratamiento de agua de la costa oeste, se utilizan productos químicos como sulfato de aluminio, amoníaco, sosa cáustica, hipoclorito de sodio y ácido sulfúrico en la coagulación y floculación para eliminar partículas sólidas y materia orgánica del agua. También se utilizan para ajustar el PH y la alcalinidad del agua.
Los productos químicos como el cloruro férrico y el hipoclorito de sodio son algunos ejemplos de ácidos que se utilizan en las plantas de tratamiento de aguas residuales. El cloruro férrico se usa para controlar los malos olores y la corrosión biogénica, y el hipoclorito de sodio se usa para desinfectar el agua tratada.
Los químicos se almacenan en tanques a granel de 5,000 a 20,000 galones dependiendo de la demanda del proceso de tratamiento. Los tanques pueden estar hechos de plástico reforzado con fibra de vidrio, acero revestido de caucho o HDPE y tienen varias bombas, tuberías, válvulas, soportes de tuberías y rejillas sobre los desagües. Ocasionalmente, los tanques o las tuberías comienzan a fallar y a tener fugas, o se producen derrames de los productos químicos durante el llenado de los tanques.
La Figura 6 muestra grietas severas en la losa del piso de un área de contención secundaria, construida en 1982, que almacena hipoclorito de sodio. Cuando una de las válvulas o tuberías falló, inundó todas las áreas de contención y los cloruros se filtraron en el concreto y hasta la profundidad del acero de refuerzo hasta 3 pulgadas de profundidad. Las concentraciones de cloruro estaban entre 500 y 3200 ppm, a la profundidad del acero de refuerzo o justo por encima. Como resultado, se crearon varias delaminaciones por la corrosión del acero de refuerzo que crea tensiones de ruptura que inducen el agrietamiento radial a lo largo de las barras una vez que se ha superado la resistencia a la tracción del hormigón.
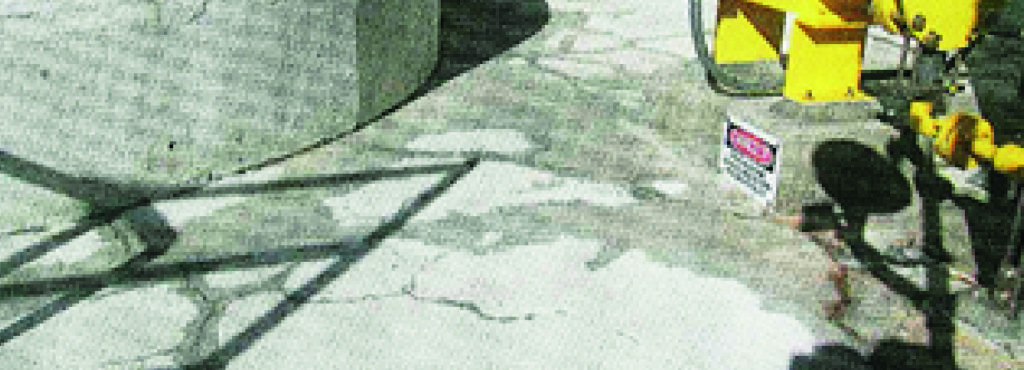
ESTÁNDARES DE LA INDUSTRIA
Cuando se observa un daño en una estructura de concreto, los propietarios quieren saber el alcance del daño y cuánto costará repararlo. Se puede realizar una evaluación de la estructura de hormigón visualmente, así como recolectando algunos satélites de la estructura si existen condiciones seguras o si un cierre de la estructura permitirá una evaluación. Los siguientes elementos proporcionarán información sobre la causa del deterioro para que pueda ayudar a los propietarios a determinar la priorización y el cronograma de reparaciones. Debido a limitaciones de tiempo y presupuesto, es posible que los propietarios no puedan solicitar la siguiente información durante una evaluación, pero se resume en este artículo con fines informativos.
Cloruros en el hormigón
Las concentraciones de cloruro en el hormigón pueden variar según el tipo de agregado utilizado, la proporción de agua a cemento, los aditivos (cenizas volantes, cemento de escoria, puzolanas naturales, humo de sílice) y la presencia de otros ingredientes de la mezcla de hormigón. Las concentraciones también variarán con la frecuencia de los ciclos húmedo-seco y las concentraciones del líquido, gas o vapor en contacto con el concreto. Las muestras de núcleos de hormigón se recogen y analizan en un laboratorio. Las concentraciones de cloruro se pueden medir de acuerdo con ASTM C1218. La Tabla 1 enumera la concentración máxima de cloruro permitida en el concreto para nuevas construcciones de varias fuentes. Se deben considerar los umbrales para monitorear y mitigar la corrosión inducida por cloruros. Por lo general, se utilizan entre seis y siete sacos de cemento para el diseño de mezclas de hormigón, y la concentración de cloruro para el hormigón de 7 sacos se muestra a continuación. Los umbrales de concentración de cloruro en porcentaje en peso de cemento se convirtieron en porcentaje en peso de hormigón para una mezcla de 7 sacos.
Profundidad de la cubierta sobre acero de refuerzo
La profundidad del recubrimiento de hormigón es un elemento importante en la protección contra la corrosión de las estructuras de hormigón armado. Cuanto mayor sea el espesor de la cubierta de hormigón, menor será la probabilidad de que los componentes corrosivos hayan alcanzado el acero de refuerzo incrustado en superficies de hormigón formado expuestas a tierra, agua, aguas residuales, intemperie o en contacto con el suelo debe ser de al menos 2 pulgadas para 6 bar o más grande y 1,5 pulgadas para 5 bar o menos. Además, según ACI 350-06, el espacio entre las barras de refuerzo para miembros rectangulares no debe exceder las 12 pulgadas para mitigar el agrietamiento.
Un método para determinar la profundidad de cobertura sobre un radar penetrante. SPR es una técnica de prueba no destructiva que utiliza ondas electromagnéticas para investigar la composición de materiales no conductores como el hormigón, ya sea al buscar objetos incrustados como acero de refuerzo y conductos, o al buscar huecos. Es más adecuado para superficies de concreto que son relativamente lisas y serían difíciles en superficies de hormigón proyectado.
La Figura 7 (P.18) muestra un ejemplo de un escaneo SPR en una superficie de concreto. El eje x es la distancia total que se escaneó y el eje y es la profundidad del objeto que se escaneó. La profundidad del acero de refuerzo se puede medir desde la parte superior de la hipérbola oscura hasta la parte superior de la losa. En la figura 7, la distancia en aproximadamente 3,1 pulgadas. En estructuras de agua y aguas residuales, es muy común ver manchas de corrosión en áreas con menos de 1 pulgada de cobertura.
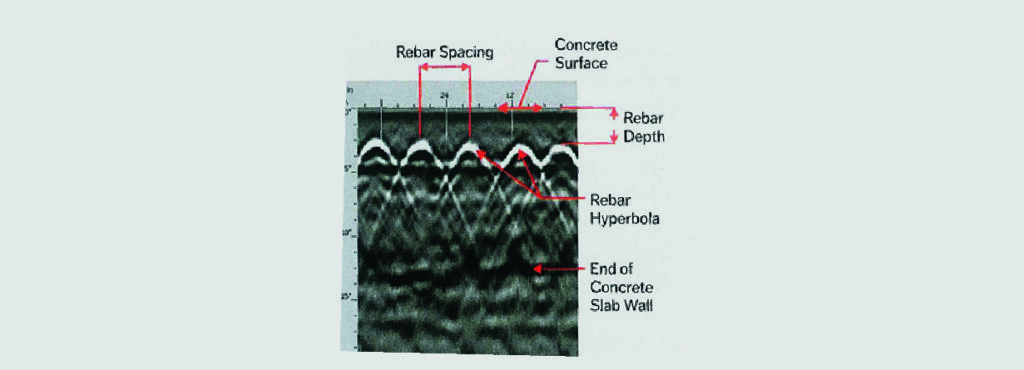
Recubrimiento
Una de las decisiones más difíciles de tomar para los propietarios es si quitar y reemplazar o repintar un sistema de recubrimiento existente. Una revisión de los estándares de la industria de SSPC y la experiencia de este autor con proyectos de recubrimiento de concreto durante los últimos 20 años ayudarán a guiar cómo el resto de la industria determina si una superficie es adecuada para repintar.
La Actualización Técnica No. 3 de SSPC se refiere a estructuras de acero; sin embargo, se revisó para obtener información sobre la evaluación de recubrimientos existentes para repintado. Dice lo siguiente:
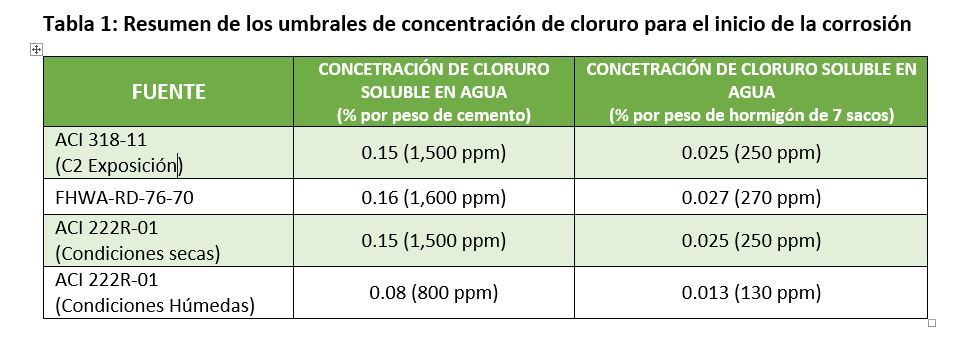
Adhesión del revestimiento: La adhesión del revestimiento existente a sí mismo y al sustrato es un factor crítico. Sin embargo, es difícil definir con precisión un valor de adhesión satisfactorio. En la actualidad, la adhesión se evalúa generalmente mediante ASTM D3359 o ASTM D4541 (sobre acero). Los sistemas que presentan valores de adhesión bajos en estas pruebas tienen más probabilidades de deslaminarse cuando se repintan que los revestimientos envejecidos con valores de adhesión más altos. Generalmente, el sistema de recubrimiento envejecido fallará en su punto más débil. El tipo de recubrimiento, la edad, el espesor y la preparación de la superficie afectan la adhesión del sistema de recubrimiento envejecido.
La Tabla 2 está tomada de SSPC TU No. 3, Apéndice A, Tabla 1: Riesgo de rescatar el revestimiento existente según las características de adherencia / espesor, que proporciona una guía para el repintado. Tenga en cuenta que ASTM D3359, Método A se usa generalmente para recubrimientos sobre sustratos de acero; sin embargo, las pruebas con cuchillo ASTM D6677 se pueden usar para pruebas de adhesión y se aplican a todas las superficies.
La recomendación general de la Tabla 2 es no repintar si los resultados de adhesión son deficientes y los espesores de recubrimiento son superiores a 20 milésimas de pulgada.
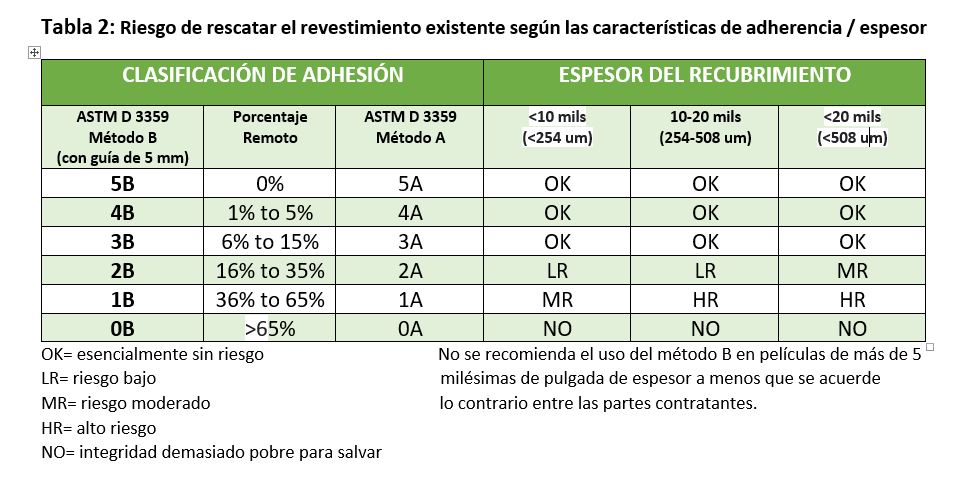
Otro recurso para determinar los requisitos de repintado es SSPC-PA 14, que se aplica a entornos de agua y aguas residuales, ya que los recubrimientos de componentes plurales se aplican comúnmente en estos entornos. Dice lo siguiente con respecto a la reparación de superficies previamente revestidas:
Reparación de superficies revestidas (Acero u Hormigón).
A menos que se especifique lo contrario, se eliminarán todos los revestimientos o revestimientos sueltos, agrietados, quebradizos o no adherentes.
La Figura 8 muestra un revestimiento existente de 30 años en un tanque de sedimentación de agua potable, que mostró una clara evidencia de fallas. Una evaluación adicional reveló que más del 30% de las superficies estaban deslaminadas y debían eliminarse.
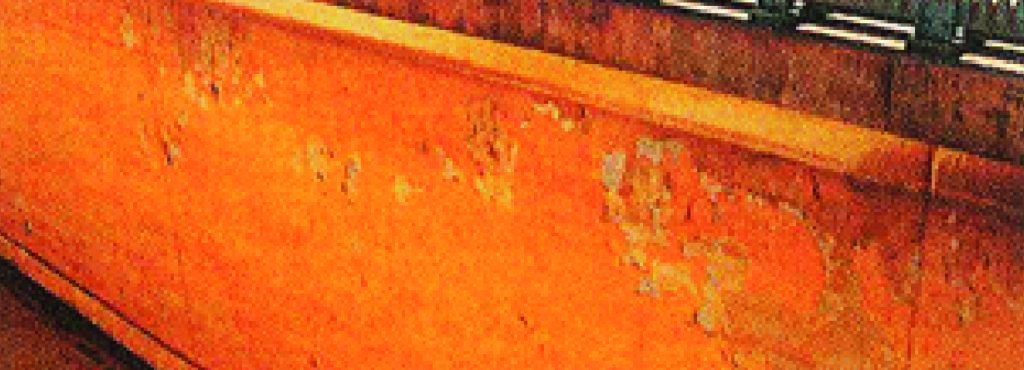
PH del hormigón
Los morteros cementosos generalmente se fabrican a partir de una combinación de agregado, arena y cemento Portland. El cemento Portland en mortero tiene un PH entre 12,5 y 13,5 a los 28 días de curado. Este nivel de PH elevado proporciona control de la corrosión para el acero de refuerzo. El acero se transformará de un estado de corrosión activa a un estado de pasividad, el cabrestante se caracteriza por una película de óxido que protege la superficie del acero está expuesta a un PH superior a 10. A un PH de menos de 10, la corrosión puede ocurrir si hay menos de 1 pulgada de cobertura en concreto sumergido o el entorno de servicio es susceptible a la corrosión biogénica.
En general, la mayoría de los fabricantes de revestimientos recomiendan que el hormigón tenga un PH de 7 o más antes de aplicar su mortero o productos de revestimiento. La escala de PH que se muestra en la tabla 3 correlaciona el efecto del medio ambiente sobre la corrosión del concreto y se deriva de la experiencia pasada y la revisión de la literatura.
PROTECCIÓN DE ESTRUCTURAS DE HORMIGÓN
Diseño de mezcla de hormigón
Antes de que se construyan las estructuras de hormigón para agua y aguas residuales, los propietarios e ingenieros de diseño deben considerar los siguientes criterios de diseño para las estructuras de retención de agua en la industria de la ingeniería ambiental.
1. Los diseños de mezcla de concreto deben tener una proporción de agua a cemento de acuerdo con las recomendaciones de ACI 318.
2. Se requiere un mínimo de 1.5 pulgadas de recubrimiento de concreto para todo el acero de refuerzo. Se requiere un mínimo de 3 pulgadas de recubrimiento de concreto en las áreas de contención secundaria cuando se almacenan cloruros.
3. Determine la vida útil de diseño requerida para la estructura y el entorno de servicio y considere agregar puzolanas como cenizas volantes o humo de sílice para prolongar la vida útil de la estructura. También se pueden agregar inhibidores de corrosión a la mezcla de concreto para extender la vida útil del concreto.
Selección de material de reparación
Hay varios productos de recubrimiento en el mercado que son químicamente resistentes al entorno de servicio en entornos de agua y aguas residuales. Sin embargo, existen varias diferencias en la flexibilidad, la tolerancia a la humedad durante las aplicaciones y la resistencia a los productos químicos entre los diferentes productos. Los productos de revestimiento deben seleccionarse para las condiciones durante las aplicaciones, además del funcionamiento normal de la estructura.
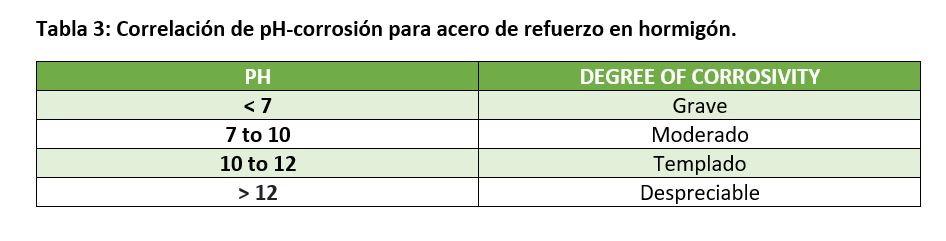
El tiempo permitido para la aplicación y curado de un nuevo sistema de recubrimiento también es fundamental para el éxito de un proyecto. En la rehabilitación de plantas de tratamiento de agua y aguas residuales o en las tuberías asociadas, hay un tiempo de parada limitado o nulo para realizar la preparación de la superficie y la aplicación del revestimiento porque hay flujo las 24 horas del día, los siete días de la semana, todo el año. El trabajo de recubrimiento en plantas de tratamiento de aguas residuales o estaciones de bombeo debe completarse porque puede haber clima húmedo en el pronóstico y las estructuras deben volver a ponerse en servicio lo antes posible para permitir una mayor capacidad de tratamiento.
La preparación de la superficie del hormigón también deberá seleccionarse en función de la edad del hormigón y el estado de la superficie. La directriz técnica 310.2 del Instituto Internacional de Reparación de Concreto proporciona normas para la preparación de superficies en forma de papel y también con muestras físicas de moldes que también se pueden utilizar en el campo. El hormigón nuevo generalmente no requiere un perfil de superficie profunda como el hormigón existente que ha sido pulido con chorro de arena. El objetivo del hormigón nuevo con chorro abrasivo es eliminar cualquier lechada, eflorescencia y superficies resbaladizas antes de aplicar el revestimiento. El objetivo de la limpieza abrasiva del hormigón existente es eliminar todo el hormigón deteriorado suelto. Si la pasta de cemento está deteriorada y el agregado sobresale de la superficie, existen al menos dos métodos para repararlo.
En proyectos de rehabilitación, el agregado expuesto se puede reparar con morteros de repavimentación o con recubrimientos especiales de alto espesor. La repavimentación del concreto se realiza en espesores de 1/8 de pulgada hasta 2 pulgadas según el nivel de degradación. Ciertos productos de recubrimiento permitirán una aplicación de hasta 250 milésimas de pulgada (6.35 mm) para cubrir algunos agregados menores expuestos en algunos casos, pero la mayoría de los fabricantes recomiendan un repavimentador.
Los defectos de la superficie en el concreto, como poros, nido de abeja, agregado expuesto, aletas y lechada deben rellenarse o eliminarse antes de aplicar un nuevo sistema de recubrimiento.
El recubrimiento sobre estos defectos superficiales puede provocar discontinuidades o una mala adherencia.
Los sistemas de revestimiento deberán seleccionarse cuidadosamente teniendo en cuenta los factores mencionados en esta sección antes de que se finalicen las especificaciones de revestimiento y se envíen a licitación. Es mejor discutir las necesidades del proyecto con un representante del fabricante de revestimientos.
Documentos de construcción
Antes de escribir una especificación de revestimiento, el especificador debe recopilar la mayor cantidad de información posible para determinar qué productos son los más adecuados para el entorno de servicio y las condiciones en las que se aplicará el revestimiento. Una buena especificación contendrá lo siguiente:
1. Límites de trabajo claramente definidos de una estructura de hormigón, incluidas las áreas alrededor de las penetraciones de las tuberías, las estructuras de puertas deslizantes y las estructuras de conexión.
2. Definición clara de lo que se considera hormigón deteriorado.
3. Profundidad del concreto deteriorado a remover para áreas sumergidas, atmosféricos interiores y otras.
4. Una descripción del nivel de preparación de la superficie requerido, como ICRI 310.2 Perfil de superficie de concreto 1 a 10 y SSPC SP13.
5. Valor mínimo de Ph para el hormigón una vez completada la preparación de la superficie, y.
6. Métodos de reparación para infiltración de agua, transiciones de superficies no revestidas a revestidas, juntas de expansión, acero de refuerzo expuesto y grietas.
Inspección in situ durante las operaciones de revestimiento
Una vez que ha comenzado la aplicación del revestimiento, el propietario y el especificador deben asegurarse de que el revestimiento se aplique según las especificaciones. Los propietarios deben invertir en un inspector de revestimiento externo que haya sido capacitado según el programa Inspector de revestimiento protector de SSPC o el programa Inspector de revestimiento NACE. Para grandes proyectos de agua y aguas residuales, el costo de tener un inspector de revestimientos es una pequeña fracción del costo total del proyecto. Para una inversión tan grande en recubrimientos protectores, se recomienda encarecidamente contratar a un inspector de recubrimientos para garantizar que los recubrimientos se apliquen según los requisitos de la especificación. Si no se puede contratar a un inspector de recubrimientos para monitorear las operaciones de recubrimiento en el campo, el propietario debe requerir que el fabricante del recubrimiento esté presente durante el inicio de la preparación de la superficie, la estrella de las aplicaciones de recubrimiento y el día de la prueba final.
CONCLUSIONES
Cuando los propietarios de tratamiento de agua y aguas residuales ven daños en sus activos, es importante recopilar la mayor cantidad de información posible antes de tomar una decisión sobre cómo rehabilitar la estructura. Es de esperar que los ejemplos del entorno de servicio presentados en este artículo proporcionen una idea de algunos indicios comunes de deterioro del hormigón. Al utilizar algunos de los estándares de la industria para la migración de cloruros, la profundidad del acero de refuerzo y los estándares de recubrimiento, estas evaluaciones pueden proporcionar información valiosa a los propietarios para justificar reparaciones costosas.
Este artículo proporcionó ejemplos de protección del hormigón antes y después de la construcción de una estructura de tratamiento. Es importante considerar el diseño de la mezcla de concreto y la selección de los materiales de reparación antes de que la especificación del revestimiento sea escrita y enviada a licitación.
Además de tener una buena especificación, también es importante tener una inspección en el sitio. Para tener proyectos de recubrimientos exitosos, los propietarios deben considerar invertir en un inspector externo que pueda proporcionar control de calidad durante las operaciones de recubrimiento.