Selección incorrecta del sistema de recubrimientos para una Torre Eólica en servicio de inmersión.
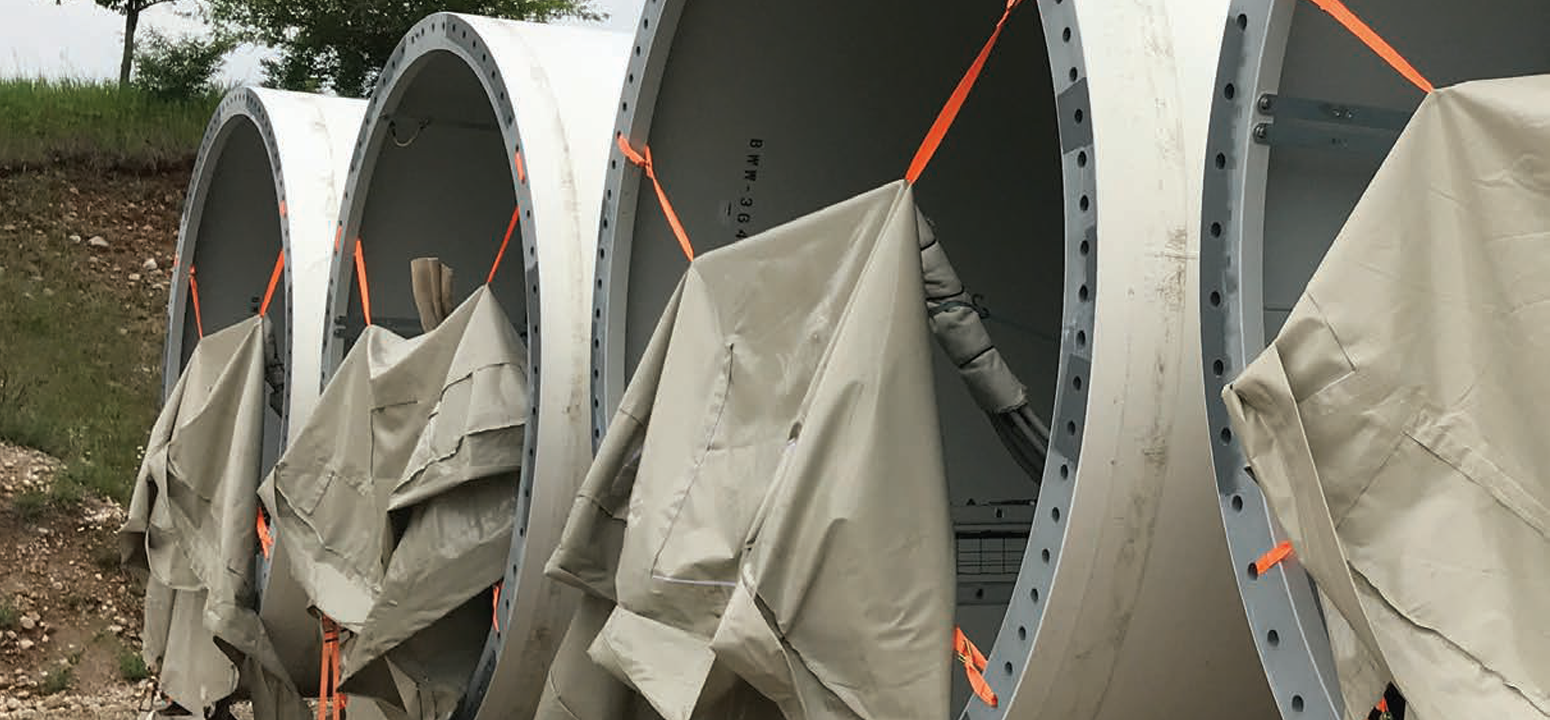
Los sistemas de recubrimientos suelen seleccionarse para proporcionar protección a un sustrato en función del entorno de servicio predominante. Irónicamente, en algunos casos el entorno más severo que el sistema de recubrimiento puede encontrar es durante el almacenamiento o el transporte de la estructura recubierta, y estas condiciones rara vez se tienen en cuenta durante el proceso de selección del sistema de recubrimiento. En este caso, el diseñador del proyecto no seleccionó un sistema de recubrimiento para una torre eólica que resistiera el servicio de inmersión.
FOTO: CORTESÍA DE KTA-TATOR, INC. / FIG. 1: Se retiraron las lonas del borde de las secciones de la torre para exponer el recubrimiento.
¿Torres eólicas submarinas? Definitivamente, esto requiere una investigación más profunda. Pero antes, detallemos un poco los antecedentes del proyecto.
Una empresa estadounidense fabricaba en sus instalaciones componentes de torres eólicas utilizando chapas de acero al carbono laminadas en caliente de diversos grosores, siendo las más gruesas las situadas en la base de las torres. Una vez que las secciones de la torre estaban completamente fabricadas, se transportaban a una zona y se limpiaban con chorro abrasivo. Las secciones cilíndricas se colocaron en un dispositivo que hace girar las piezas mientras una unidad de granallado centrífugo limpia la superficie con una mezcla de granalla de acero. A continuación, las secciones de la torre se limpiaron manualmente con granalla abrasiva en ambos extremos.
FOTO: CORTESÍA DE KTA-TATOR, INC. / FIG. 2: Ampollas claramente visibles en el recubrimiento cerca del borde del recubrimiento retirado.
Las torres eólicas se fabricaron para varios clientes diferentes, y los sistemas de recubrimiento utilizados en las torres variaron según el fabricante. El sistema de recubrimiento utilizado en las superficies exteriores de las torres fabricadas para un cliente consistía en una capa de imprimación epoxi rico en zinc, una capa intermedia de epoxi a base de solvente y una capa final de poliuretano.
Las bridas del extremo de las secciones de la torre y las superficies de acero al carbono de 12 pulgadas inmediatamente adyacentes a las bridas fueron metalizadas en lugar de imprimadas con zinc. Las zonas que se recubrieron con imprimación rica en zinc debían limpiarse mediante chorro abrasivo de acuerdo con la norma SSPC-SP 10/NACE nº 2, Near White Metal, “metal casi blanco” con una profundidad de perfil superficial de 2 a 3,5 mils. En las zonas donde se había aplicado el metalizado, la superficie debía limpiarse mediante granallado de acuerdo con la norma SSPC-SP 5/NACE n.º 1, Metal blanco, con la misma profundidad de perfil de superficie.
FOTO: CORTESÍA DE KTA-TATOR, INC. / FIG. 3: Un patrón de pequeñas ampollas estaba presente bajo las correas que aseguraban la cubierta.
La ficha técnica del recubrimiento intermedio de epoxi indicaba que el recubrimiento se recomendaba como imprimación en ambientes atmosféricos de suaves a medios y como recubrimiento intermedio o de acabado en ambientes atmosféricos de corrosión media a severa. En la ficha técnica del producto también se afirmaba que podía utilizarse directamente sobre superficies metalizadas. La capa de acabado se describía en la ficha técnica del producto como una capa de acabado de poliuretano acrílico semibrillante de dos componentes, curada con isocianato alifático.
Una vez aplicados los recubrimientos, las piezas se trasladaron a un lugar exterior. Después de dejar secar y curar los recubrimientos, los extremos de las secciones de la torre se cubrieron con lonas especialmente fabricadas para ajustarse a los extremos. Las lonas se fijaron firmemente con correas integrales de nailon tensadas con cabrestantes(winches). Las lonas se dejaron en su sitio mientras las secciones estuvieron almacenadas, lo que osciló entre unas pocas semanas y más de un año.
Se observaron ampollas en el recubrimiento antes de que los componentes abandonaran el patio de almacenamiento. El fabricante de torres eólicas contrató a un consultor independiente de recubrimientos para determinar la causa de las ampollas.
Investigación en campo
Se realizó un examen de las secciones de torre recubiertas en un depósito situado a unos kilómetros de la planta de fabricación. Antes del examinación, se retiraron las lonas que estaban sujetas a los extremos, dejando al descubierto los extremos exteriores de las secciones de la torre.
FOTO: CORTESÍA DE KTA-TATOR, INC. / FIG. 4: Cuando se retiró el revestimiento a la fuerza y se chorreó con abrasivo, aún quedaban restos de metalizado al descubierto.
El exterior de las secciones de la torre estaba pintado con un recubrimiento blanco. Salvo algunas excepciones, el recubrimiento estaba intacto y no presentaba defectos visibles.
El recubrimiento parecía haberse ampollado en algunas zonas cerca de los extremos de las secciones de la torre. La formación de ampollas se producía normalmente en un patrón circunferencial en la sección principal de la torre a pocos centímetros de la soldadura que conecta las secciones principales de la torre con las bridas. En la mayoría de los casos, había un patrón de suciedad en la superficie que indicaba que las ampollas se habían producido directamente debajo de donde la lona estaba sujeta a las secciones de la torre con las correas de nailon. Con una excepción, las ampollas estaban totalmente intactas y no había grietas asociadas en el recubrimiento del borde de las ampollas. Se encontró una ampolla que tenía una grieta en el recubrimiento en un borde.
Se retiraron las ampollas en varias zonas, lo que reveló que el plano de delaminación en la zona ampollada se encontraba entre el metalizado y la superficie de acero al carbono. En el momento del examen, no había líquido visible en la ampolla.
En todos los casos, al retirar los recubrimientos en una zona ampollada, la superficie de acero quedaba expuesta y había un perfil angular profundo visible en la superficie. También había manchas negras visibles, en diversos grados, en las superficies de acero expuestas. Las manchas eran de color negro oscuro, más oscuras de lo que normalmente se encuentra en la cascarilla de delaminación, y generalmente de 1 milímetro o menos de diámetro. La superficie bajo una de las ampollas retiradas tenía numerosos puntos negros pequeños, pero no suficientes para cubrir más del 10% de la superficie del acero. Bajo otra de las ampollas muestreadas, la superficie presentaba 4 ó 5 pequeños puntos negros. Bajo una de las ampollas, la superficie del acero estaba libre de puntos negros.
Se retiró la ampolla que se había agrietado en el borde de la tapa. Al igual que en las demás ampollas, el plano de delaminación se encontraba entre el metalizado y la superficie del acero. El centro de la ampolla presentaba un depósito de óxido negro y rojo.
El sistema de recubrimiento se eliminó a la fuerza de las zonas en las que no había ampollas cortando el recubrimiento con una navaja multiusos, realizando cortes paralelos muy próximos entre sí. Las tiras de recubrimiento se eliminaron en su mayor parte hasta dejar el acero desnudo, pero en general quedaban restos del metalizado en la superficie que eran claramente visibles al observar la superficie con magnificación.
Investigación de laboratorio
La investigación de laboratorio consistió en un examen visual y microscópico y un análisis espectroscópico por infrarrojos. El examen microscópico reveló que las zonas de fallo contenían normalmente cinco capas, y no las tres especificadas. La última capa era el metalizado. Las dos capas adicionales parecían ser una superposición de la imprimación rica en zinc y epoxi que se aplicó inmediatamente adyacente a la zona donde se aplicó el metalizado. En todos los casos, las cinco capas parecían estar intactas y bien adheridas entre sí y no se consideraron un factor en el fallo del recubrimiento. El examen microscópico también reveló que había un producto de corrosión blanco en la superficie posterior del metalizado retirado. El material tenía el mismo aspecto que los productos de corrosión del zinc y era claramente el resultado de la corrosión del metalizado. En algunos casos, el producto de corrosión blanco era relativamente grueso y había algo de óxido de hierro rojo visible.
FOTO: CORTESÍA DE KTA-TATOR, INC. / FIG. 5: En algunas zonas, debajo de las ampollas se apreciaba óxido rojo y corrosión blanca del zinc.
El análisis espectroscópico por infrarrojos reveló que tanto la capa intermedia como la de acabado tenían una composición coherente con los recubrimientos especificados. Los bordes de las muestras que se retiraron para el análisis de laboratorio se curvaron una vez secas.
Conclusiones
Las investigaciones de campo y de laboratorio llevaron al investigador a la conclusión de que la causa de los pequeños puntos de delaminación del sistema de recubrimiento de las secciones de la torre eólica era la excesiva transferencia y absorción de agua en y a través del sistema de recubrimiento en zonas donde el agua de lluvia quedaba atrapada en la superficie del recubrimiento por las lonas. Era evidente que el agua había penetrado bajo la lona impermeable y que ésta impedía que el agua se evaporara, creando una zona en la que el agua estaba continuamente en contacto con el sistema de recubrimiento.
La delaminación del sistema de recubrimiento apareció en forma de ampollas que se desarrollaron en el sistema de recubrimiento en las zonas de los extremos de las secciones de la torre que estaban cubiertas por lonas. Durante la visita a la obra, se observó que las ampollas se producían predominantemente donde las correas de nailon sujetaban las lonas.
La delaminación se produjo en forma de ampollas en el recubrimiento, pero las ampollas no eran las típicas que se suelen encontrar en inmersión. Las ampollas que se forman en el servicio de inmersión suelen estar causadas por sales solubles en la superficie o disolventes solubles atrapados en el recubrimiento. El agua atraviesa el recubrimiento mediante un proceso denominado ósmosis para diluir las sales solubles o los disolventes hasta alcanzar el equilibrio. El líquido de la ampolla se acumula en la superficie y crea una contrapresión que provoca la ampolla en el recubrimiento. Está claro que en este caso no se produjo ampolla osmótica, ya que no había una cantidad significativa de agua en las ampollas.
Había numerosos indicios de que una cantidad significativa de humedad fue absorbida y transferida a través del sistema de recubrimiento. El examen microscópico de laboratorio indicó que había una importante corrosión visible en la parte posterior del metalizado que se retiró con las muestras. La corrosión era visible en forma de manchas blancas algo translúcidas en la parte posterior del metalizado y podía encontrarse incluso en muestras en las que no se había producido delaminación. Generalmente, cuando se aplica un sistema epoxi de buen rendimiento sobre el metalizado, la absorción y transferencia de humedad a través del epoxi es bastante lenta.
Las secciones que se examinaron durante la visita a las obras llevaban recubiertas aproximadamente un año. Después de un año, cabría esperar una corrosión mínima del metalizado. Recordemos que las muestras retiradas para el análisis de laboratorio se curvaron en los bordes cuando se secaron. Esto es una clara indicación de que las muestras habían absorbido una cantidad significativa de humedad y se habían hinchado como resultado. Una vez evaporada la humedad de las piezas, la tensión de contracción hizo que los bordes se curvaran. Este fenómeno es extremadamente inusual y, por lo general, sólo se produce cuando se toman muestras de una pintura a base de solvente poco después de haberla aplicado y dejado secar. Una vez que el recubrimiento se retira por la fuerza, el solvente que quedó atrapado en el recubrimiento se evapora por la parte posterior expuesta y la muestra se encoge, creando tensiones que provocan el rizado de los bordes. La curvatura de los bordes en un revestimiento que se ha dejado curar durante un año indica una absorción significativa de humedad.
La delaminación del recubrimiento sólo se produjo en las zonas donde se aplicó el metalizado. El fabricante de torres eólicas aplicó el metalizado alrededor de las zonas de las bridas para dos clientes; el fallo del revestimiento sólo se produjo en las torres eólicas suministradas a uno de esos clientes. La preparación de la superficie y la aplicación del metalizado fueron idénticas en ambos casos. La única diferencia significativa fue el sistema de pintura. El recubrimiento aplicado a las secciones de torre que fallaron era un epoxi curado con aducto de poliamida. El recubrimiento aplicado a las otras secciones de la torre era un epoxi curado con aminas. Se sabe que los epoxis curados con aminas tienen mejor resistencia al agua y a los productos químicos que los epoxis curados con aductos de poliamida. El uso del epoxi curado con aminas sobre el metalizado de las secciones de la torre que no fallaban impidió sin duda que se absorbiera suficiente humedad en el sistema de recubrimiento y que ésta se transfiriera a través del mismo como para provocar la delaminación del recubrimiento.
La transferencia de humedad hacia y a través del sistema de recubrimiento en los extremos de la sección de la torre provocó la delaminación del recubrimiento por absorción en la capa de epoxi, haciendo que se hinchara. El hinchamiento creó una presión ascendente sobre el sistema de revestimiento y provocó el desprendimiento del metalizado. Además, la transferencia de humedad a través del metalizado algo poroso hizo que el metalizado se corroyera hasta cierto punto en la interfaz entre el metalizado y la superficie de acero al carbono, lo que afectó negativamente a la adhesión. Estos dos fenómenos se combinaron para crear pequeñas zonas de fallo de adhesión. Se cree que este fallo sólo pudo producirse cuando el recubrimiento estuvo en contacto casi constante con el agua. El agua atrapada bajo las lonas (donde éstas estaban sujetas) creaba un entorno de inmersión constante.
ACERCA DEL AUTOR
Rick Huntley es el Director técnico de servicios de consultoría y consultor senior de recubrimientos de KTA-Tator, Inc. Tiene más de 30 años de experiencia en prevención de la corrosión, recomendaciones de sistemas de recubrimientos, investigaciones de fallos de recubrimientos y apoyo en litigios. Huntley es inspector de recubrimientos certificado por la NACE de nivel 3 (revisión por pares) y especialista en recubrimientos protectores certificado por la SSPC. También es instructor principal de varios cursos de formación de la KTA, instructor aprobado por la SSPC NBP1 y licenciado en Ingeniería Química por la Universidad Estatal de Washington.
Fuente: JPCL
Traducción al idioma español – Actualización: IARCOR INTERNACIONAL